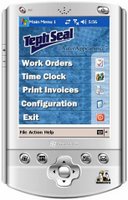
We completed a mobility project for a Canadian company last week that adds hybrid electrical components to delivery trucks. I found this very interesting. We used standard consumer grade PDAs, MobileDataforce's Intercue Mobility Suite and RS232 adapters to plug into an automobile's computers and read OBD-II Trouble Codes. These codes could be uploaded to a database and printed in a report. Reading your vehicle's vitals with a PDA just seems so futuristic to me.
There is an OBD-II Trouble codes plug-in under the dashboard of most vehicles. With this application a mechanic can quickly identify any errors or problems being reported by the automobile's sensors. The results can be displayed on a handheld PDA screen and printed to a report.
In past blog articles I have written about our ability to decode VIN numbers and build powerful automobile inspection applications, for dealers, buyers, and automotive services companies all on handheld computers. Now we have added the ability to inspect the condition of the engine.
In another article I wrote some time back I discussed connecting GPS capture to automotive applications. This was needed to identify the location of abandon cars following hurricane Katrina.
In summary you can do a whole lot with a PDA in the automotive sector. Here are a few application features we have delivered:
- VIN Decoding on a PDA to identify the details of a specific car
- Engine inspection and error decoding with a PDA
- Attaching work orders and service orders to specific VIN numbers using a PDA
- Combining GPS coordinates with a VIN number on a PDA
- Using a bar code scanner on a handheld computer to capture VIN numbers
- Printing invoices on a mobile printer that combine VIN numbers with work orders
- Automotive inspections and valuations of automobiles using a handheld computer